How Timely Packaging Machine Repair Can Prevent Costly Downtime
How Timely Packaging Machine Repair Can Prevent Costly Downtime
Blog Article
Quick and Reliable Product Packaging Maker Repair Work Solutions to Minimize Downtime
In the competitive landscape of production, the performance of packaging procedures depends upon the dependability of machinery. Quick and reputable repair services are important in reducing downtime, which can lead to substantial monetary losses and operational problems. Recognizing the significance of prompt interventions and the duty of professional technicians can change how services come close to repair and maintenance. However, browsing the myriad choices readily available for fixing solutions can be challenging. What aspects should businesses think about to guarantee they are making the right option for their functional needs?
Importance of Timely Services
Timely repairs of product packaging equipments are crucial for maintaining operational effectiveness and lessening downtime. In the hectic atmosphere of manufacturing and product packaging, also minor breakdowns can cause significant delays and productivity losses. Dealing with issues immediately makes certain that makers run at their ideal capacity, thereby guarding the flow of operations.
Moreover, timely and regular upkeep can stop the escalation of minor troubles into major failures, which usually sustain higher repair prices and longer downtimes. A positive approach to equipment repair service not only maintains the stability of the equipment yet likewise enhances the general reliability of the manufacturing line.
Furthermore, timely repair services add to the long life of packaging equipment. Makers that are serviced promptly are much less likely to experience from excessive damage, allowing organizations to maximize their financial investments. This is especially vital in industries where high-speed product packaging is important, as the demand for consistent efficiency is paramount.
Advantages of Reliable Company
Trustworthy solution carriers play a crucial duty in ensuring the smooth procedure of product packaging machines. Their proficiency not only enhances the efficiency of fixings yet additionally adds dramatically to the long life of devices.
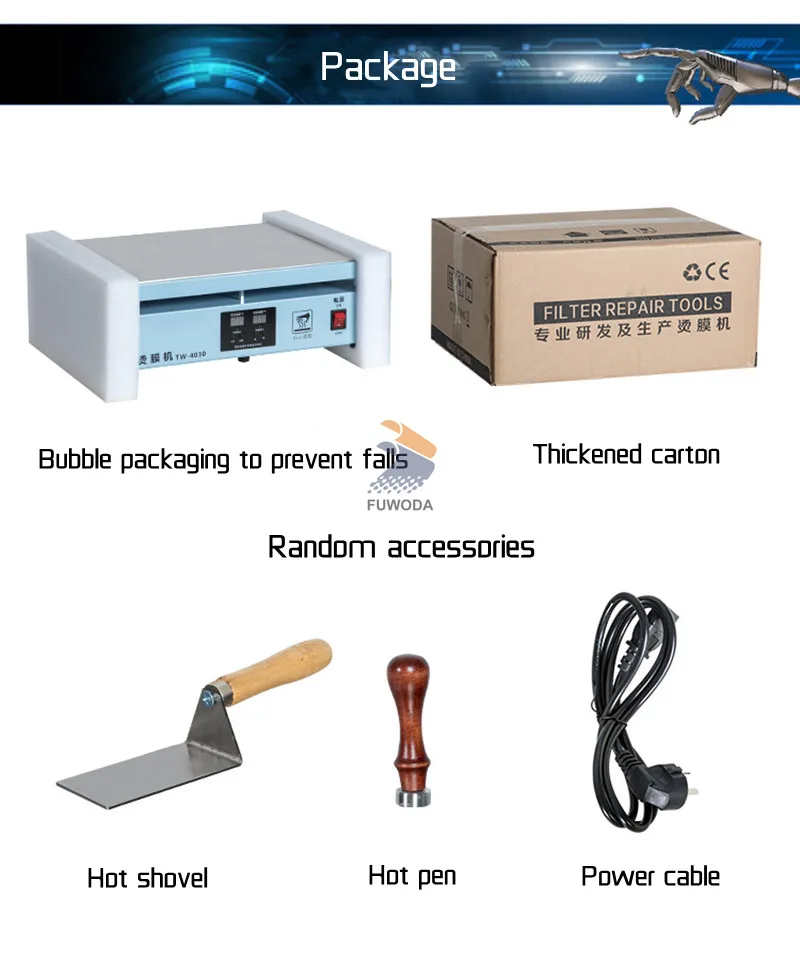
Furthermore, a credible company uses detailed support, consisting of training and guidance for staff on device procedure and upkeep finest methods. This not only equips employees but also grows a society of safety and security and effectiveness within the organization. In general, the benefits of involving reliable solution carriers extend past prompt repair services, positively impacting the whole functional process of packaging procedures.
Typical Packaging Machine Concerns
In the world of packaging procedures, different problems can compromise the performance and performance of devices. One widespread issue is mechanical failure, often originating from deterioration or inadequate upkeep. Components such as belts, motors, and gears might stop working, bring about malfunctions that halt manufacturing. Another typical issue is imbalance, which can cause jams and unequal product packaging, affecting item high quality and throughput.
Electrical troubles can also interrupt product packaging procedures. Defective wiring or malfunctioning sensors might cause erratic maker actions, causing delays and boosted functional costs. Furthermore, software program problems can hinder the device's programs, bring about operational inefficiencies.
Inconsistent item flow is another important problem. This can arise from variants in product form, weight, or dimension, which might impact the machine's capability to handle things precisely. Ultimately, inadequate training of operators can exacerbate these troubles, as untrained employees might not recognize early signs of malfunction or may abuse the devices.
Attending to these common packaging equipment issues quickly is important to keeping performance and making sure a smooth procedure. Routine evaluations and proactive upkeep can dramatically minimize these click over here worries, cultivating a reliable product packaging setting.
Tips for Lessening Downtime
To reduce downtime in packaging procedures, carrying out a positive upkeep approach is vital. Frequently scheduled upkeep checks can determine potential concerns before they escalate, making sure devices run effectively. Establishing a regimen that includes lubrication, calibration, and examination of vital components can dramatically decrease the regularity of unforeseen failures.
Educating personnel to run machinery appropriately and acknowledge early indication of malfunction can also play an essential role. Empowering operators with the expertise to carry out standard troubleshooting can avoid small issues from triggering significant delays. In addition, maintaining an efficient supply of vital extra parts can speed up fixings, as waiting for parts can bring about extended downtime.
In addition, documenting device performance and upkeep tasks can aid recognize patterns and persistent issues, permitting for targeted treatments. Incorporating advanced tracking innovations can provide real-time data, web allowing anticipating upkeep and lessening the threat of abrupt failings.
Last but not least, cultivating open interaction in between drivers and upkeep groups makes certain that any kind of abnormalities are without delay reported and addressed. By taking these proactive measures, businesses can enhance functional performance and dramatically lower downtime in product packaging procedures.
Selecting the Right Repair Service Service
Choosing the suitable repair solution for product packaging makers is an essential choice that can substantially impact operational efficiency. An appropriate company guarantees that your machinery is fixed quickly, efficiently, and to the highest criteria. Begin by examining the supplier's experience with your certain kind of product packaging devices. A service technician aware of your equipment can identify issues extra precisely and implement remedies a lot more rapidly.
Next, take into consideration the provider's track record. Seeking feedback from other businesses within your sector can offer understandings into dependability and quality. Accreditations and partnerships with acknowledged tools producers can additionally indicate a commitment to quality.
Additionally, evaluate their feedback time and availability. A provider that can offer timely assistance decreases downtime and keeps production circulation constant. It's also essential to ask concerning warranty and service assurances, which can mirror the self-confidence the service provider has in their work.

Final Thought
Finally, the value of dependable and fast packaging machine repair service services can not be overemphasized, as they play an important role in lessening downtime and guaranteeing functional efficiency. By focusing on timely fixings and choosing reputable provider, companies can properly deal with usual problems and keep performance. Executing aggressive upkeep methods and buying team training additional improves the longevity of packaging equipment. Inevitably, a tactical technique to fix services promotes a much more resistant production atmosphere.
Prompt fixings of packaging machines are important for preserving operational effectiveness and lessening downtime.Furthermore, prompt repair services add to the durability of packaging machinery. In general, the benefits of engaging dependable service providers extend past prompt fixings, favorably affecting the entire operational workflow of product packaging procedures.
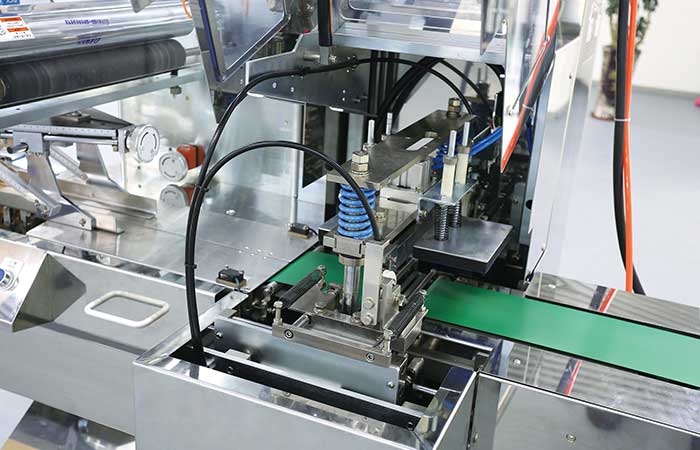
Report this page